محمدعلی شبیری - خبرماشین - ایران خودرو در تلاش است با تعریف پروژه هایی در داخل مجموعه که برخی از آن ها نیز از گذشته تاکنون وجود داشته در بحث کاهش قیمت تمام شده و ارتقای بهره وری و داخلی سازی قطعاتی که پیش از این از طریق واردات تامین می شد نسبت به کاهش قیمت سربار و هزینه تولید اقدام کند.
به لحاظ درآمدهای اقتصادی، حوزه صنعت در بسیاری از بخش ها زیان ده است و قابل رقابت با صنایع دیگر دنیا نیست؛ اگر قرار باشد به حوزه های بین الملل وارد شد باید کارها و فعالیت های جدی در این زمینه انجام تا این صنعت در قسمت های مختلف متحول شود. به کارگیری روش های مختلفی برای کاهش هزینه ها و افزایش درآمدزایی به این موضوع کمک خواهد کرد.
بخشی از این هزینه ها ناشی از تولید و دپوی خودروهای ناقص بوده است. گروه صنعتی ایران خودرو با تغییر رویکرد از تولید خودروهای ناقص به عبور مستقیم محصولات از ماه های پایانی سال گذشته گام مهی در مسیر بهبود کیفیت، رشد عرضه و کاهش هزینه های سربار ناشی از مراجعه مشتریان به شبکه خدمات پس از فروش برداشته است.
از طرفی شرکتهای تابعه سرمایهگذاری ایرانخودرو، باید نقش واقعی خود را بهعنوان یک بنگاه اقتصادی برای ارتقای کیفیت تولیدات و خدمات، کسب سود و توسعه بازار محصولات، بهصورت جدی در دستور کار قرار دهند. اصلاح ساختار و فرآیندها در شرکت های خودروساز و حذف شرکت های غیر ضروری فرعی تابعه باعث جلوگیری از انتقال عمومی سود از شرکت اصلی به شرکت های فرعی می شود. بنابراین با اصلاح ساختار و فرآیندها در شرکت های خودروساز و حذف شرکت های فرعی و انتقال وظایف و کارکرد و تجمیع آنها در یکی از معاونت های ذی ربط از زیان ده شدن این شرکت جلوگیری خواهد کرد.
عرضه خودروهای بی کیفیت یکی دیگر از مواردی است که با حذف آن می توان به کاهش هزینه ها کمک کرد؛ این موضوع علاوه بر افزایش نارضایتی مشتریان، زمینه رشد هزینه سربار شرکت های خودروسازی در شبکه خدمات پس از فروش و به خصوص دوره گارانتی را افزایش می دهد. البته با تغییر سیاست های این گروه صنعتی، حل این معضل آغاز شده و آمار کاهش مراجعه به نمایندگی ها به منظور تعویض قطعات گواه این موضوع است.
انتقال دانش بین شرکت های داخلی و خارجی و استفاده از محصول ها و دانش یکدیگر و بومی سازی این دانش در سایه اعمال دقیق مدیریت دانش، امکان پذیر خواهد بود. از طرفی گسترش و تقویت فعالیت های تحقیق و توسعه ای( R&D )، گسترش مراکز تست و کنترل کیفی و تهیه و تدوین استانداردهای اجباری و نظارت بر حسن اجرای آن ازجمله مواردی هستند که در رضایت مشتری و در پی آن در جهت توسعه صادرات موثر خواهد بود.
یکی از مشکلات اصلی گروه صنعتی ایران خودرو تامین قطعات بوده که راهکار برون رفت از این مسئله، قدرت گرفتن شرکت های زیر مجموعه مانند ساپکو با ماموریتهای جدید در حوزه تأمین قطعات متناسب با شرایط، تامین به موقع با هزینه کم و کیفیت بالا است. در حال حاضر در بسیاری از کشورها شرکتهای واسطهای بهدلیل افزایش هزینه خرید و همچنین بوروکراسی زیاد، توسط خودروسازان بینالمللی از چرخه تامین حذف شدهاند و جای آنها را مجموعه سازان یا هلدینگهای قطعهسازی) گرفته اند. در واقع هلدینگهای قطعهسازی که به آنها OEM میگویند، وظیفه تامین قطعات را برای شرکتهای خودروساز بر عهده گرفتهاند.
در صورت ایجاد هلدینگ های قطعه سازی، هزینه های خودروسازی به شکل چشمگیری کاهش می یابد چرا که قطعه سازان نسبت به ایجاد هلدینگ های خود اقدام کرده و قطعات از طریق یک منبع به خودروساز تحویل داده می شود که در این شرایط شاهد حذف واسطه ها و هزینه های زاید خواهیم بود.
علاوه بر موارد فوق، دو خودروساز بزرگ میتوانند با تولید و تامین مشترک قطعات اصلی خودرو، به میزان قابلتوجهی در هزینههای خود صرفهجویی کنند. در حال حاضر شرایط بهگونهای نیست که دو خودروساز بزرگ کشور بخواهند با همکاری یکدیگر پلتفرم مشترک تولید کنند، بلکه باید ابتدا بر تولید مشترک قطعات اصلی خودرو تمرکز کنند. بهعنوان مثال هر کدام از این دو شرکت بهصورت جداگانه در حال طراحی و تولید یک موتور جدید با راندمان بالا و مصرف سوخت پایین هستند، این پروژهها با یکدیگر ادغام شده و با همکاری دو طرف یک موتور ملی برای استفاده هر دو شرکت تولید شود.
در همین راستا اخیراً سایپا و ایران خودرو در راستای همکاری های استراتژیک خود، اقدام به امضا تفاهمنامه توسعه همکاری های مشترک در زمینه موتور و گیربکس کردند. بر این اساس تامین 10 هزار موتور خودرو شاهین برای مدت یک سال به صورت مشترک انجام می شود و بدین منظور موتور TUP و گیربکس 6 دنده اتومات در پلتفرم شاهین استفاده می شود.
همچنین درتحقیق و توسعه طراحی خودرو و قوای محرکه نیاز به آزمایشگاه ها و دستگاه هایی است که ایجاد آنها بسیار هزینه بر است و در همکاری استراتژیک این مورد دیده شده که دو شرکت از توان موجود یکدیگر استفاده کرده و نتیجه آن افزایش کیفیت محصول خواهد بود.
علاوه بر آن در صورت تولید مشترک قطعات اصلی خودرو از سوی دو خودروساز یزرگ کشور، تیراژ قطعات تولیدی به شدت افزایش یافته و به همان نسبت هزینههای تمام شده آن کاهش مییابد. قطعاتی مانند موتور، گیربکس، اکسل، سیستم فرمان، سیستم ترمز و جعبه دنده از قطعات اصلی تشکیلدهنده پلتفرم خودرو است که در حال حاضر این دو شرکت خودروساز هر کدام بهصورت جداگانه کار طراحی، تولید و تامین این قطعات را انجام میدهند.
کاهش هزینه تولید راهکارهای متنوع و مختلفی را میتواند داشته باشد از جمله اینکه هزینه مواد اولیه و قیمت تمام شده آنها با استفاده از سازوکارهایی که در اختیار قانون گذار است مانند تعرفه گمرکی و نظایر آن کاهش یابد. شرایط کشور ما خاص و متفاوت از شرایط باثبات کشورهایی است که با ظرفیت های بالا در خودروسازی فعال هستند. نوسانات سریع نرخ ارز و نرخ تورم هر برنامه ریزی را با شکست مواجه می کند و یا از تاثیرپذیری آن می کاهد. البته دولت هم باید بسته سیاستی مناسبی را برای مدیریت جریان نرخ ارز بر قیمتها و کاهش هزینه تولید ارائه دهد. با حمایت دولت چنانچه هرگونه افزایشی در نرخ ارز و هزینهها صورت میگیرد انتظار میرود شاهد کاهش هزینه تولید باشیم.
حذف قیمتگذاری دستوری خودرو، تقاضای سرمایهای (دلالی) را که بر اساس اختلاف قیمت کارخانه و بازار شکل گرفته، به شدت کاهش میدهد و از طرفی دیگر عرضه خودرو را به دلیل به صرفه بودن تولید برای تولید کننده، افزایش میدهد؛ موضوعی که برآیند آن در کاهش قیمت مصرفکننده خودرو تاثیر زیادی دارد.
راهکار دیگر در جهت کاهش قیمت تمام شده خودرو، انجام فعالیت های مهندسی است. در مهندسی ارزش، بر روی کاهش قیمت تمام شده کار می شود. امروزه به شدت نیازمند این فعالیت هستیم و توانمندی آن در شرکت های خودروسازی وجود دارد. خودروسازان می توانند با ارائه طرح های جدید در جهت کاهش هزینه تمام شده قدم بردارند.
در چنین شرایطی، از آنجا که صنعت خودروسازی سود ده میشود، در بلندمدت نیز سرمایهگذاران را برای سرمایهگذاری در حوزههای خودرو، قطعات و توسعه صنایع تکمیلی مربوطه جذب می کند؛ در مجموع به افزایش بهرهوری، کاهش هزینهها و افزایش عرضه خودرو منجر میشود.
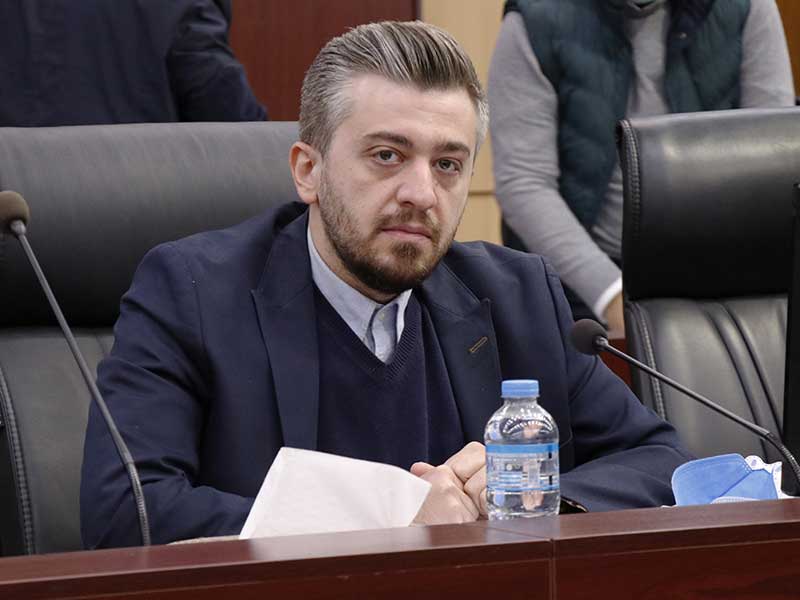